News
Production moving to the U.S.
In order to improve our Global presence in the production of Cross Wedge Rolling and other forging equipment, ERS Engineering Corp. is excited to announce that beginning March 1st, 2023, we are opening a manufacturing site in Almont, Michigan to support our North American market.
By bringing our production to the U.S., we will eliminate any supply chain uncertainty and will ensure continued excellence in customer service. A similar manufacturing site in Europe will be opening soon
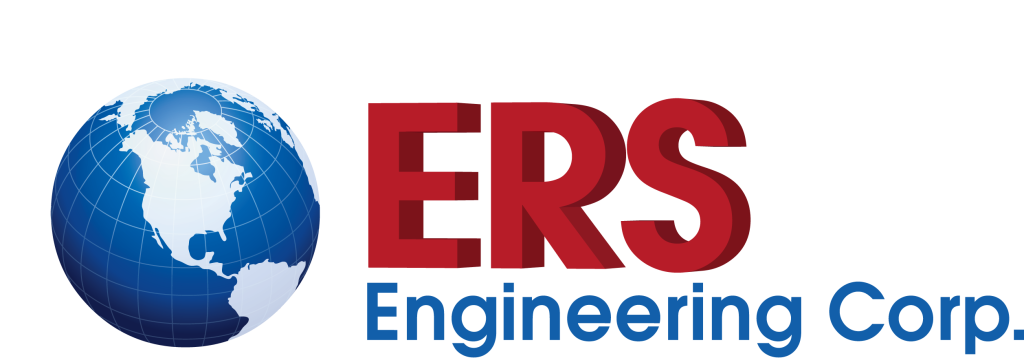
Our team at ERS Engineering wants to wish you and your family a Merry Christmas and Happy New Year 2022!
Kessler & Co. GmbH appoints ERS Engineering Corp. to be their Sales Consultant in the Russian territories.
ERS Engineering Corp. will act as an Independent Sales Consultant of Kessler.
ERS will market, facilitate and promote Kessler’s products to potential customers and aid in sales negotiations.
Kessler manufactures axles, wheel drives, transmissions and other mechanical power-train products for use in a variety of industrial and commercial equipment worldwide.
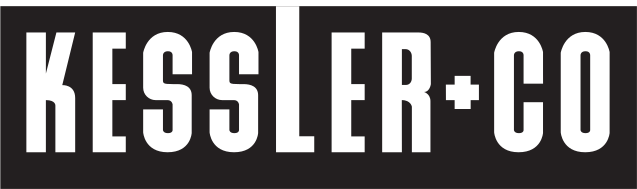
ERS Engineering is talked about in this issue of Forge Magazine. Emerging Technology for Manufacturing Rail Axles.
ERS Engineering to represent MJC
ERS Engineering Corp. is pleased to announce that we are officially the exclusive distributor of MJC Engineering & Technology, Inc. in the territories of the Former Soviet Union (FSU).
For nearly two decades, MJC’s team of innovative and experienced experts have been designing, manufacturing and supporting advanced CNC Metal Spinning Equipment for customers across the globe. MJC is a world leader in spinning and flow forming machines for the wheel industry.
ERS Engineering Corp. has over a decade of cooperation with AMT Engineering and has a very strong reputation with solid connections on this market. With AMT Engineering’s strong engineering and production capability we will provide all the necessary support in sales, marketing and servicing to ensure successful supply of MJC Engineering & Technology, Inc. products on the Former Soviet Union (FSU) territory.
ERS Engineering Corp. to announce a formal agreement with the Lublin University of Technology (LUT) located in Poland.

Semyon Brayman – President of ERS Engineering Corp.
Zbignev Pater – Head of Mechanical Engineering Department of LUT
Alexander Roudovich – General Manager of AMT Engineering
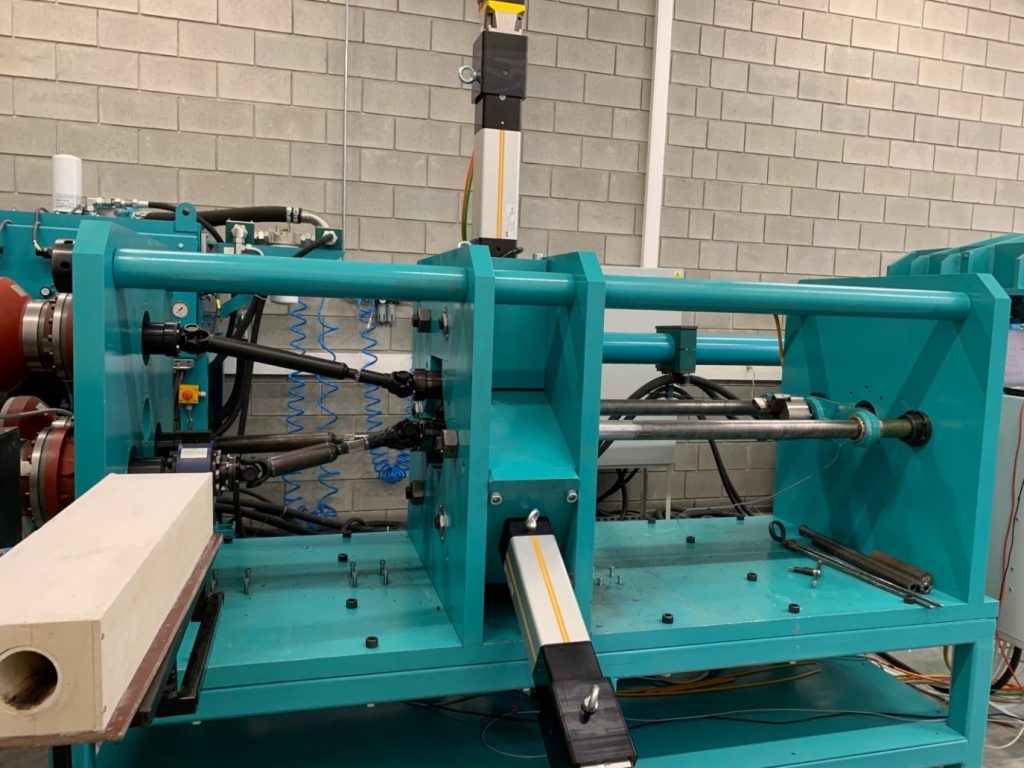
The Lublin University of Technology was established as the Evening Engineering School in May 1953 on the initiative of Lublin technical societies. The first department that began its activity in 1953 was the Mechanical Engineering Department.
The Evening Engineering School was converted into the High Engineering School on April 28, 1965.
And, finally, the auspicious day for the University was August 1, 1977 when the Lublin University of Technology was established.
The Lublin University of Technology offers cooperation with the industry in the following areas:
- Design and implementation of metal forming technology, in particular cross-wedge rolling (CWR), wedge-roller rolling (WRR), screw-wedge rolling (SWR), die forging, rotary thrust, rotary crimping and enveloping pressing. The offer also includes designing of the required production equipment.
- Design, implementation and development of technologies based on CWR, WRR and SWR, among others: rolling hollow products, rolling products with a non-round cross-section, rolling rail axles, rolling balls (e.g. for bearings or grinding mills) using the CWR and SWR method.
- Development of free and matrix forging technology (in open and closed matrices) taking into account the material shaping specifics.
- Process design. Shaping forgings of a complex shape. The development of the technology includes forging on conventional forging machines (crank presses, hydraulic presses, screw presses, forging machines, etc.) as well as using specialized machines – e.g. forging on a three-stroke press.
- Increasing the durability of tools used in conventional and unconventional methods of plastic forming.
- Development of new, specialized metal shaping technologies, including designing of machines, instruments and tools.
- Performing multivariate numerical simulations using the finite element method (FEM) and the finite volume method (MOS). LUT can also develop their own computer software that will implement engineering computational methods to support the processes of designing metal forming processes.
Our ultimate goal is close cooperation with the industry focused on solving difficult problems. The result of scientific work is not only the development of new technologies but also designing, manufacturing and commissioning of the required forging equipment.
“The cooperation with Lublin University of Technology [LUT] is a very important step in the development of presence of Cross Wedge Rolling technology on the North American market.
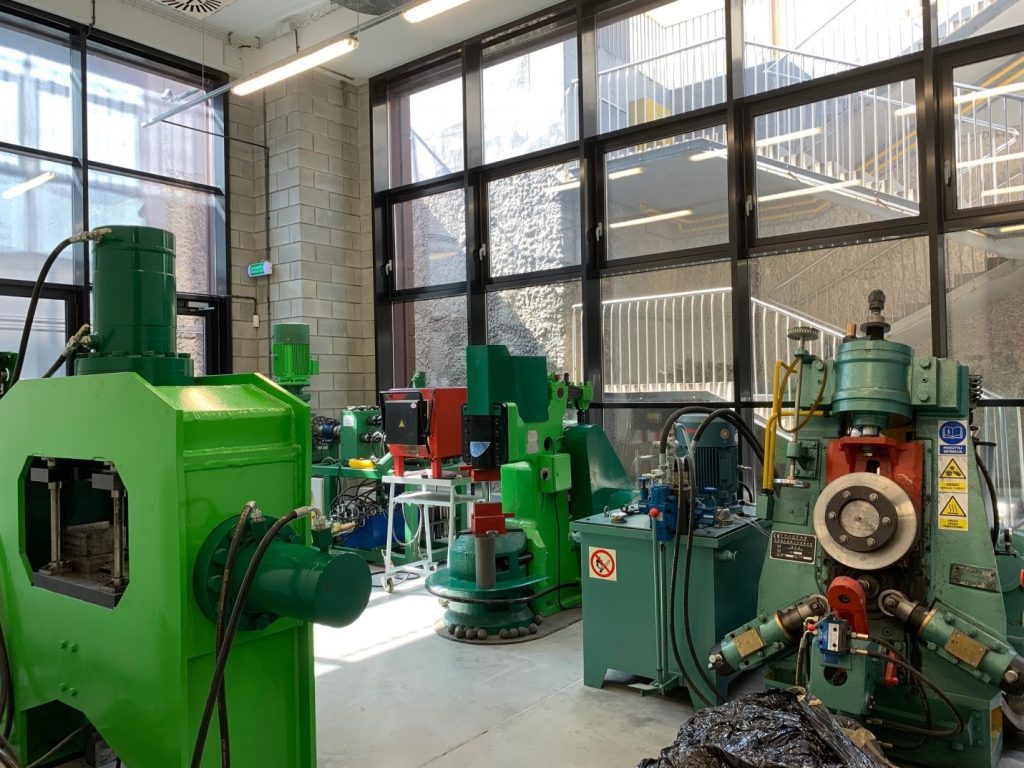
With LUT’s capability in engineering, process development, and prototyping, AMTengineering manufacturing experience and knowledge of the forging industry, and ERS Engineering Corp. experience in sales and support of this type of equipment, we can offer solutions for any kind of requirements from the simple ones to the most complicated,” says Semyon Brayman, the president of ERS Engineering Corp.